Gyraf Audio G9
Welcome to the Gyraf Audio G9 DIY Page....
08. Jan. 2007
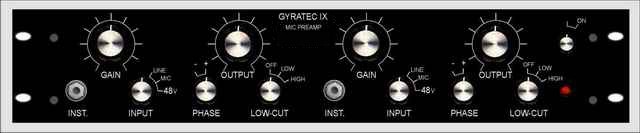
Do-It-Yourself G9 Tube Microphone preamplifier
The G9 project is an adaptation of the Gyratec IX dual microphone/line/DI preamplifier to suit the DIY'ers demands. Searching the net, I've never come across a complete tube microphone preamp design, so I decided to share this version of our very popular design, the Gyratec IX. It is a classic, conservative design, that easily matches the performance of even the most expensive and esoteric units I've been able to compare it to.
I wish to thank Kev and Byron from Group DIY for test-piloting this project, and for their changes and comments on the original design. Without those guys this level of DIY-friendlyness would'nt have been even remotely possible.
Take a look at how Kev Ross builds this project Kev and Byron's page on building the Gyraf G9.
The G9 contains two channels of real-tube, high-gain, transformer-balanced microphone preamplifiers with additional line and instrument inputs and transformer balanced output. It also features switchable phantom power, high-pass filter and phase reverse, as well as independent controls for input gain and output level - giving the user some creative options to work with.
The signal path contains only tubes, transformers and passive components, to preserve your signal integrety. VERY different from many "tubed" consumer products. But as we are not purists, we incorporate modern semiconductors in the powersupply sections - simply because this is way the easiest, cheapest and best solution available. For power amplifiers there's quite an audible reason to use tubed power supplies, but for preamps I haven't been able to spot any advantage so far.
I will try to update this page reguarly if anyone shows interest in its topics. Comments and corrections are extremely welcome, but I can't promise to reply to all mail I receive. In "The Lab" - a forum on GroupDIY.org - there will surely be people that can and will answer most of your questions regarding the design, construction, and sourcing of parts. If you build this project and describe elements of the process, I'll be more than happy to add it - or a link to it - here, so others can benefit from your experiences.
Disclaimer:
Notice that all information, schematics, layouts etc. are supplied "as is", and that we can in no way be held responsible for its acurateness, functionality or even safety. Gyraf Audio shall not be responsible and disclaims all liability for any loss, liability, damage (whether direct or consequential) or expense of any nature whatsoever, which may be suffered as a result of, or which may be attributable, directly or indirectly, to the use of or reliance upon any information, links or service provided through this website. Now you know that..
Basic safety rules:
You have to take extreme caution when working with Mains and High Voltages. These voltages are lethal, and even the smallest error will be chatastrophic. And we like you to stay alive and well, so you can help other people sharing our bizarre interest for building retro-pro-audio-equipment.
- NEVER work with live voltage switched on. Switch off, discharge, work, connect measuring equipment and power up. The G9 powersupply takes an average of 15 minutes to come down to non-dangerous voltages, providing that the tubes has had a chance to get hot. But if there's something really wrong, the lethal HT can stay for weeks! TAKE CARE!! ALWAYS positively measure HT voltage on the PSU caps before touching ANYTHING. A good idea is to have a resistor, like 10K/2W, on a cable with two clips that you can attach to the caps for discharging. But please. Remember. Take care.
- Always keep your mains connector in plain sight when working, so you can assure yourself that it really is disconnected.
- Always tidy up your working area before connecting your project to the mains. This gives you some time for second thoughts about what you are doing.
The Schematic:
As you can see from the schematic, the G9 is really a VERY simple, no-nonsense tube mic pre. Click on the schematic for a high-resolution version, suitable for printing
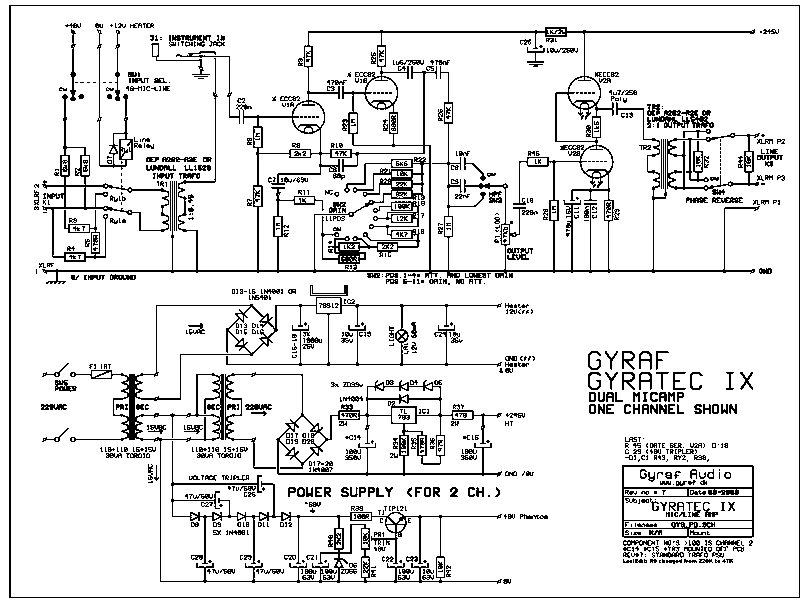
Circuit description:
The input is taken to Phantom resistors and the line input relay. The line relay - as well as the Phantom power - is controlled by the front panel rotary switch, SW1: (line - mic - mic+p48). When in "line" mode, we set the input attenuation to -26dB, the Zin to~10KOhm - but still Z-matched to the transformer, with an option of either OEP A262-A3E or Lundall 1528.
Note that OEP's HAS to be in screening cans, including the output trafos (that are not canned on the pictures, sorry). Without it, I've had oscillation problems because of the high gains and bandwidths involved.
The secondary of the input trafo is taken through a switched "instrument" jack plug on the front of the unit. Very nice for guitars, basses and keyboards (and fantastic for a Mellotron if you happen to come across one..) - and then to the input gain stage, based on an ECC82 (12AU7, 5814 etc..).
The input gain stage is pretty much a standard feedback gain-controlled circuit like the ones used in all old tube audio gear. It's gain is controlled by shunting the fed-back AC signal on V1a's cathode to ground - think of it as a opamp gain block with 47K (R10) from output to inverting input. You can now control the circuit's gain by shunting the inverted input to ground - through a cap, C7, because we don't want to disturb the DC cathode potential, made by R6 and R7, setting bias in V1a. C7 also protect our gain switch, SW2, from destruction by DC..
The only tricky part in this is the gain switch, normally divided into one feedback switch and one attenuation switch.. But - you know I like the simplicity, availability and easy mounting of the "Lorlin" type switches - so I had to think a little here.. and came up with this "grounded common" switching scheme, actually performing two different tasks:
On the first 4 steps, the lowest gains of the gain switch, the system gain is kept to minimum - only R12 (1M) shunting to ground to avoid DC build up in C7, our 10uF/63V polyester AC cathode shunt cap - and the output of the gain stage is attenuated by R26 (47K) and either of R19-22 (5K6-82K).
On the highest gains - the steps 5 through 11 on SW2 - attenuation resistors R19-22 are taken out of circuit, and AC cathode-to-ground shunt resistors R13-18 (1K-100K) becomes active, rising the gain.
The now gain-controlled signal is taken to the high pass filter, a simple passive 6dB one around C8,9 and SW3 - and then to the "output gain", a 47K log pot feeding the output driver stage.
The output driver is a 18dB gain SRPP stage, also using an ECC82 tube. It drives the output transformer - either OEP A262-A2E or Lundall 5402 - through a 4u7/250V polyester DC blocking output cap.
The output trafo is wired 2:1 to get the 2400 Ohms Zout of the SRPP stage down to around 600 Ohms. The 2:1 ratio means that when using the OEP 1+1:2+2 transformer, it has to be reversed. I've had very good results using this output stage topology in all sorts of designs - it's simply my favourite tube circuit. Also used in the Gyraf Pultec amplifier.
The output of the transformer is taken to SW4, the phase reverse switch, that has 10K resistors across it to control transformer load when switching. And then to the output XLR.....
The Power Supply:
The power supply is right off the book.
The 245v HT is made from 220V/50mA ac, rectified and regulated by IC1, a TL783 high voltage regulator. The TL783 is limited to max. 120V in-to-out differential voltage, so the three 39V zener diodes (D3-5) protect it from voltages higher than this. Also the 1N4004 (D2) protects it from lower voltage on the input than on the output, a condition it hates.
Note that for space, the two 100u or 220u/350V (C14-15) HT reservoir capacitors are mounted off-board, in chassis mount collars, and can be anything from 100 to 470uF, minimum 350V DC.
The output voltage of the regulator is set by the ratio of R34 and R36+36, to about 245VDC, keeping us within the range of 250V capacitors. The HT directly drives both output stages, and is filtered by C25/R31 for the input stage.
The 12V for the heaters is derived from 15V/1A ac, rectified, and regulated by IC2, a 78S12 1.5A voltage regulator. The heater voltage is also used for controlling the line relay, RY1. Note that the 78S12 regulator dissipates quite a lot of power - around 5W - and MUST be mounted (electrically isolated) on a good heat sink, preferably with thelmal contact to the chassis. I use a heavy aluminum angled profile that is mounted to the bottom of chassis (see pics). It would also be possible to mount the 78S12 on three (short, heavy) wires, and bolt it to the chassis back - electrically isolated. Failing to heatsink the 78S12 appropiately will result in thermal shutdown - you'll loose the 12V lines whenever the unit heats up.
The 48V phantom is also relatively straight-forward: It's a zener regulated design, adjustable with PR1, and fed from a voltage tripler running off the 15V that goes from the first transformer to the second.
The PSU Transformers:
You need two 220:15+15V 1A (30VA or larger) toroid transformers, the first converting 220v to 15v - for the heater and through the tripler to P48 - and the other one converting the 15V also used by the tripler back to 220v for the HT.
For 110V mains, you'll need two 110+110:15+15V (30VA or larger) toroid transformers. The two first primaries - for mains input - should be coupled in parallel, for 110V. The two primaries of the second transformer should be connected in series, to bring voltage up to around 220Vac.
Note that:
· Toroid transformers should definitely be used here, as the mic preamp is a quite sensitive unit.
· Main PCB size is 150x209 mm, one half of a standard 21x30 pre-sensitised PCB.
· Control PCB size is 100x160mm standard size pre-sensitised PCB, that - after etching and drilling - has to be cut into three pieces. Two control boards, and a spare psu. The spare PSU is just because I had the extra space anyway, and I find that having extra HT+ Heater PSU's laying around greatly helps tube creativity.
· PCB is - as always - drawn reversed, i.e. as seen from component side. Refer to PCB-side text if you're in doubt.
· On the PCB layout, component numbers larger than 100 denotes components for channel 2.
All components should be easily available, and the unit requires no other trimming than the phantom voltage set to 48V.
The Components list:
Here's the latest updated shopping list. However, there's no guarantee of correctness (yet..), so you better check out for yourself if it's sensible..
g9_components.txt - the shopping list.
The PCB Artwork:
These are the PCB layouts for the G9 dual micpre. They're contained in a 510KB PDF-file to maintain scale - just remember NOT to use the "fit to page" option in acrobat when printing.
As always, the track side is shown mirror'ed - as seen from component side - for better copying onto photoresist PCB's. The set consist of two pcb's, one 15x21cm - the main board, and one 10x16cm, the control board.
The main board is straight-forward, but the smaller control PCB has to be cut into three sections; two sets of front-panel controls and one (BONUS!) spare HT+Heater voltage PSU for your further tube experiments. This is both because the space was there anyway, and because I think that the hard thing getting started with when working with tubes is - the powersupply.
510KB .PDF document with layouts and component placement (rev#5).
Mikkel C. Simonsen of TechTalk has helped me with the conversion to Gerber files - for those of you who don't want to make the pcb's yourself:
377KB .ZIP-file with layouts and drill-files in Gerber format.
It's easiest to save this to your harddisk by "rightclicking" the link, and selecting "save target as.."
The construction process:
First of all a warning: This is not a project that is suitable for the
beginner. If you haven't worked with tubes and high voltages before, I'd
recommend that you start out with something simpler than this preamp.
I'll leave up to you how to mechanically construct the unit, but there's a few
points that are important:
- When mounting the Toroid power transformers, make sure that the centre bolt
that holds them is only touching the chassis in one end. This is really
important, because if the centre bolt touches hhassis in both ends, you are in
fact adding an extra, shorted winding to the transformers..
- Keep the PSU transformers as far away as possible from the audio
transformers - specially the input transformers. Also keep your distance from
the front panel, as the "output gain" is somewhat highohmic and hence
sensitive. A good way of working is to leave transformer mounting to the very
last step in construction - after all other is working and can be checked.
With the preamp running, move the PSU transformers around in the box (WATCH
WHERE YOU PUT YOUR HANDS!) to find the spot where they're intefering the
least. Mark the spot, and mount the transformers here..
- Connect 0V/Gnd to chassis at one - and only one - point: At the input XLR's.
- Connect the power ground from the power inlet to the ground at the input XLS's also.
- If you experience oscillation at extreme gain settings, try using shielded wire to/from the instrument input jack on the front. This is the first wires of the group of five that connects main board to control board.
The Mechanics:
This project is designed to be mounted in a 19" 2U rack case. Because of the way the control PCB is laid out, you'll need to follow a front panel layout like this:
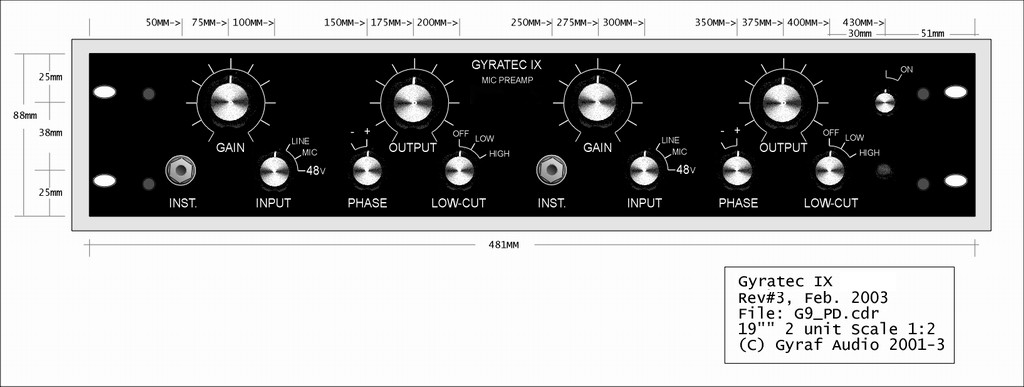
The G9 project is designed to fit into a 19" 2U rack case, and laid out to fit
a 19"2U frontplate. Off course it would be possible to use all sorts of
enclosures with some creativity, but you'll have to change quite a lot of the layouts to do so. I'd
recommend that you go with the original solution.
The frontplate drawing shows where to drill the holes for the controls -
remember to measure twice and drill once, not the other way around.
You'll get the most precise results if you start with small drills and
gradually work your way up to the right size. Drilling with a large drillbit
from start dosen't work! For the XLR's you'll need either a tapered "multicut"
stepped drill, or a set of manual hole punches. The most used sizes for XLR's
are 20mm for XLR M and 24mm for XLR F.
For the Power IEC-connector it's a bit more complicated. First mark up clearly
the needed contour on your back plate, drill a row of closely-spaced 3mm holes
all way around inside this perimeter, take a handheld drill and - carefully -
move from side to side to cut the material between the holes. Once you've
removed the material from the centre, the rest is a matter of filing down to
the needed size. Hard work, but not complicated...
For front panel marking, I've always liked engraving - but that's easy for me
as I happen to have an engraving machine in my workshop.
Other options could be having a frontplate engraved from an engraver, or
ordering from "Shaeffer Apparatebau" that makes custom frontplates from CAD
drawings. If you happen to make up a S.A. CAD-file for the G9 - and you're
willing to share it - I'd very much like to have a copy here for other
constructors. But please have it made first, so we're sure that it is working alright.
A simpler and cheaper solution is to mark the front with white "Letraset"
transfers and covering with laquer.
Or marking the front with a pencil - in handwriting - and using a hand-held
engraver like a "Dremel" to engrave it. I did this before I got my Gravograph.
Still another solution is using a blank frontplate in stead of the black one.
With this you could simply laser-print the needed frontplate marking (in
reverse!) on to a semi-transparant plastic film, and stick the plastic film to
the frontplate using a sheet of double-sided adhesive tape. With your printed
text and markings on the inside of the plastic film, this is very long-lasting
compared to the letraset solution. I think Farnell has the double-sided
adhesive type of sheet/tape.
Pictures of the G9:
NOTE: This is an early unit, with minute differences from the current DIY-version
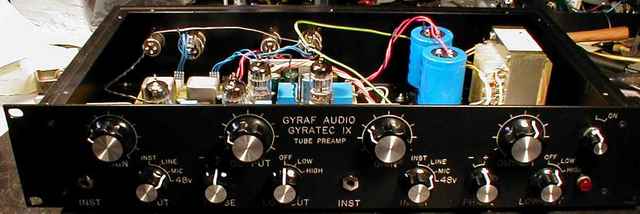
The G9 as seen from the front..
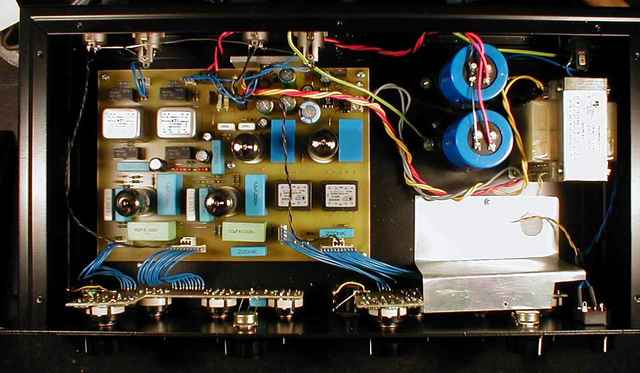
G9 top view..
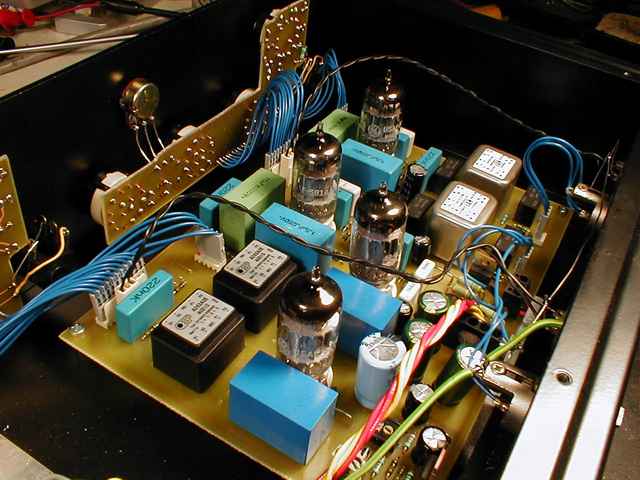
The main PCB and one control PCB..
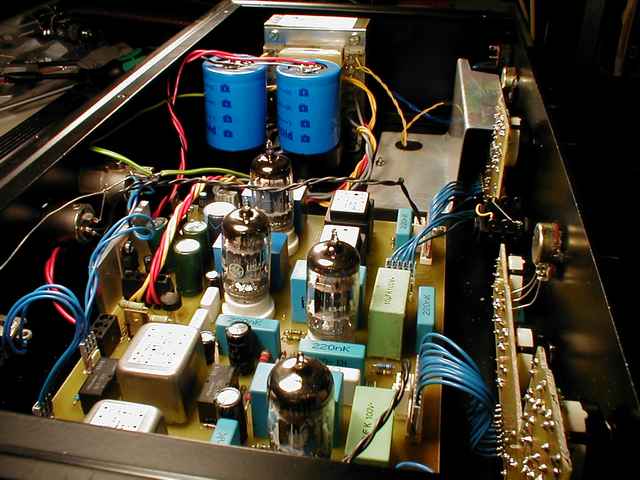
G9 overview. The mu-metal plate at ch.2 is for shielding. It should be unnecessary when using toroid transformers.
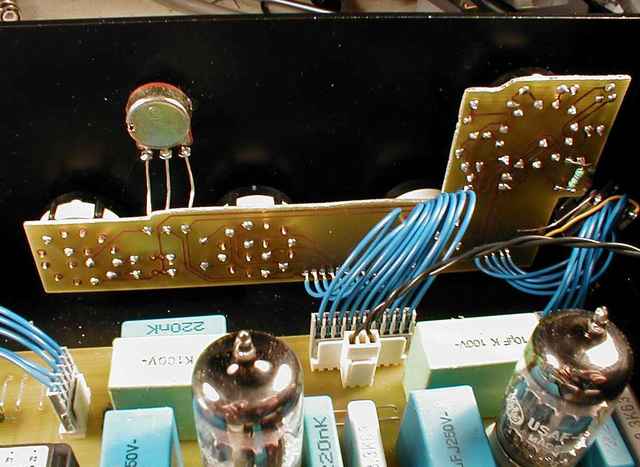
Closeup of one of the control PCB's.
If problems arises, errata and changes will be posted on this page.
ERRATA:..
02-02-2003: Original drawings
28. March. 2003: R9/109 changed from 220K to 47K to prevent oscillation problems
25. May 2003: D15/D16 was missing a connection on PCB rev#3. New PCB's are now rev#5.
09. mar. 2004: MCS's Gerber files added.
08. Jan. 2007: If you run into problems with oscillation on the highest gain settings, try running the connections to/from the front panel High-Z jack connector "directly" from the relevant points on the PCB - by cutting the PCB traces, and running a length of shielded cable directly to/from the jack. See this image for reference!!
If you let me know how you're managing this project - and if you have information that could interest other diy-people - I could link to it, or I could put it on this page. Share your information. It really wants to be free.
In the meantime, check out Kev Ross' DIY-Page on Recording.org, with a description and a "builders guide" for this project:
Kev's and Byron's G9-diy page from the old GroupDIY-pages
The GroupDIY forum "The Lab" is a good place to ask questions about this project:
http://www.groupdiy.org/
...there's a good chance you will find me hanging around there...
G9-Specific forum at "The Lab"
Paul S. has built a nice "retro look" version of this project:
http://home.houston.rr.com/lpstephan/g9_mic_pre.htm
Some other relevant links:
RafaelFreddy's Pultec MB1 project
Tubetech MP1A - schematic
HOME
Shown:
02-2003
Jakob Erland
08-01-2007